SUPPLIER QUALITY
APQP, PPAP and FSIL Supplier Requirements
APQP - Advanced Product Quality Planning
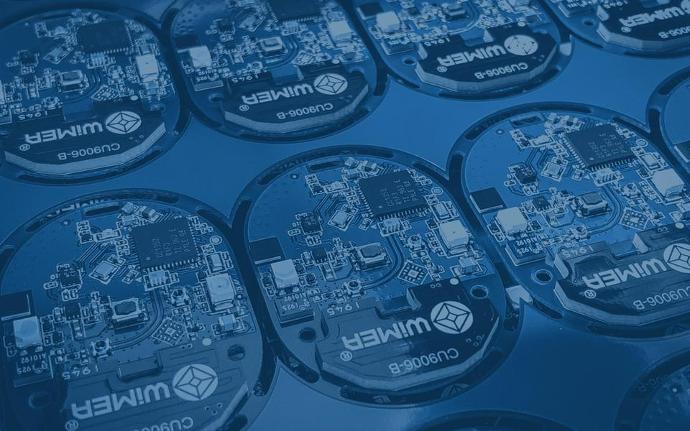
Supplier APQP and PPAP Training Document
This training document is created to educate and guide our valued suppliers through the Advanced Product Quality Planning (APQP) and Production Part Approval Process (PPAP). The purpose is to ensure that all suppliers understand and can effectively implement these processes, ensuring product quality and consistency, in alignment with Fell Tech's high standards and requirements.
Introduction
APQP is the primary Quality Management System in Fell Tech for the Product Development and Engineering Processes.
As a supplier for Fell Tech, it's essential to understand and comply with our required quality processes when they are included in the purchasing or Purchase Order requirements. Two key processes that may be required are the Advanced Product Quality Planning (APQP) and the Production Part Approval Process (PPAP).
Advanced Product Quality Planning (APQP) is a framework of procedures and techniques designed to ensure that the products we develop meet customer needs, expectations, and requirements. It helps to establish a quality plan with the steps to design, develop, and deliver products that satisfy customer expectations. APQP promotes a shared understanding of the necessary steps to ensure that the product development process runs smoothly, on time, and on budget.
On the other hand, Production Part Approval Process (PPAP) is a standardized process in the automotive and aerospace industries that helps manufacturers and suppliers communicate and approve production designs and processes before, during, and after manufacture. PPAP ensures that the processes used to manufacture parts can consistently reproduce the parts at stated production rates during routine production runs.
At Fell Tech, we use these processes to ensure the quality and reliability of the products we purchase from our suppliers. Therefore, we may require you to carry out APQP and PPAP based on the specifics detailed in our Purchase Order requirements. Compliance with these requirements will help in building a strong, reliable, and quality-focused supplier relationship. Please review these processes thoroughly and implement them as needed.
- Advanced Product Quality Planning method to assure that a product satisfies the customer (both internal and external)
- The goal of APQP is to:
- Plan before acting
- Anticipate and prevent issues
- Validate before moving forward
- Facilitate communication
Each Advanced Product Quality Plan is unique and is a living document
Particular emphasis should be placed on identifying critical path activities and ensuring those are fully resourced
APQP Benefit
Manufacturing process functions that are clearly planned, validated, documented and communicated that result in:
- Robust and reliable designs
- Reduced process variation
- Enhanced confidence in supplier’s capabilities
- Better controlled process changes
- Defect free launches
- Improved Customer satisfaction
- Improved Delivery and Service
- Maximum ROI
- Minimum Waste
- Minimum Cost of Non-Conformance (CONC)
What are the APQP Development phases?
The Advanced Product Quality Planning process consists of four main phases and five major activities and has some 20+ supporting tools (e.g. DFMEA, PFMEA, CTQ, Special Characteristics, Control Plan, SPC) along with ongoing feedback assessment and corrective action. The phases below is an illustration of a standard APQP process. Fell has developed a specific APQP process and Program Phase Requirements, that can be found here PDE Program Phase Requirements.
All phases needs to go through a Gate Review. The Gate Reviews has predefined check points and necessary documents, tests and validation points that is set for each Gate. The content of the Gate Reviews are determined for each project and determined for each Gate prior to starting a new Phase.
Illustration: Standard Fell APQP Program Timing Chart and Phase Overview.
Validation and Review stages
The stars in the above Timing Chart and Phase Overview illustrates project reviews. These stars indicate a validation of a deliverable, e.g. a prototype or a group documentation for the phase. Typically both. These reviews are always prior to a Gate Review, as the documentation and results from these reviews form the output data going into the Gate Reviews.
- CV = Concept Validation
- DV = Design Validation
- PV = Production Validation
Phases | Scope | X-F Review | X-F Review Goal |
---|---|---|---|
Phase 0 | Input and evaluation | - | Agreement to develop initial business opportunity |
Phase 1 | Definition and planning | - |
|
Phase 2 | Design and Concept Development | Concept Review (CV) |
|
Phase 3a | Design Compatibility | Design Compatibility (DCM) |
|
Phase 3b | Design Validation | Design Validation Review (DV) |
|
Phase 4 | Process Validation | Production Readiness |
|
Phase 5 | Launch | Launch Readiness |
|
1. Plan and Define Program
Purpose
Assure that customer needs and expectations are clearly understood.
Inputs
- Voice of the Customer
- Market Research
- Historical Warranty and Quality Information
- Team Experience
- Business Plan/Marketing Strategy
- Product/Process Benchmark Data
- Product/Process Assumptions
- Product Reliability Studies
- Customer Inputs
Outputs
- Design Goals
- Reliability & Quality goals
- CONC targets
- Preliminary Bill of Materials
- Preliminary Process Flow Chart
- Preliminary list of Special Product and Process Characteristics
- Product Assurance Plan
- Management Support
*The inputs and outputs applicable to the process may vary according to the product process and customer needs and expectations.
Input and Output Documentation
As part of the FELL Quality Management System all relevant templates for the Input and Output documentation is available in Confluence. Typically these are already structured in a project space as part of the tree structure of pages in a project. The easiest way to know that you are selecting a correct template is to only create templates from the "Click To Create" buttons on pages within a project space.
2. Product Design and Development
Purpose
Develop design into a near final form.Prototype and feasibility studies – volumes, schedule, manufacturing.
Inputs
- Design Goals
- Reliability & Quality goals
- Preliminary Bill of Materials
- Preliminary Process Flow Chart
- Preliminary list of Special Product and Process Characteristics
- Product Assurance Plan
Outputs
- Design Failure Mode and Effects Analysis (DFMEA)
- Design For Manufacturability and Assembly
- Design Verification
- Design Reviews
- Prototype Build – Control plan
- Engineering Drawings (Including Math Data)
- Engineering Specifications
- Material Specifications
- Drawing and Specification Changes
*The inputs and outputs applicable to the process may vary according to the product process and customer needs and expectations.
3. Process Design and Development
Purpose
Develop a manufacturing system and its related control plans to achieve quality products.
Inputs
- Design Failure Mode and Effects Analysis (DFMEA)
- Design For Manufacturability and Assembly
- Design Verification
- Design Reviews
- Prototype Build – Control Plan
- Engineering Drawings (Including Math Data)
- Engineering Specifications
- Material Specifications
- Drawing and Specification Changes
- New Equipment, Tooling and Facilities Requirements
- Special Product and Process Characteristics
- Gages/Testing Equipment Requirements
- Team Feasibility Commitment
- Management Support
Outputs
- Packaging Standards
- Product/Process Quality System Review
- Process Flow Chart
- Floor Plan Layout
- Characteristics Matrix
- Process Failure Mode and Effects Analysis (PFMEA)
- Pre-Launch Control Plan
- Process Instructions
- Measurement Systems Analysis Plan
- Preliminary Process Capability Study Plan
- Packaging Specifications
- Management Support
*The inputs and outputs applicable to the process may vary according to the product process and customer needs and expectations.
4. Product and Process Validation
Purpose
Validate manufacturing process through production trial run.
Validate that the control plan and process flow chart are effective and that the product meets customer expectation.
Inputs
- Packaging Standards
- Product/Process Quality System Review
- Process Flow Chart
- Floor Plan Layout
- Characteristics Matrix
- Process Failure Mode and Effects Analysis (PFMEA)
- Pre-Launch Control Plan
- Process Instructions
- Measurement Systems Analysis Plan
- Preliminary Process Capability Study Plan
- Packaging Specifications
- Management Support
Outputs
- Measurement Systems Evaluation
- Significant Production Run
- Preliminary Process Capability Study
- Production Part Approval (PPAP Submission)
- Production Validation Testing
- Packaging Evaluation
- Production Control Plan
- Quality Planning Sign-Off - formal
- Management Support
*The inputs and outputs applicable to the process may vary according to the product process and customer needs and expectations.
5. Feedback, Assessment, Corrective actions
Purpose
Evaluate outputs, effectiveness of the product quality planning efforts.
Inputs
- Production Trial Run
- Measurement Systems Evaluation
- Preliminary Process Capability Study
- Production Part Approval
- Production Validation Testing
- Packaging Evaluation
- Production Control Plan
- Quality Planning Sign-Off and Management Support
Outputs
- Reduced Variation
- Improved Customer Satisfaction
- Improved Delivery and Service
- Effective use of best practice, lessons learned
- Maximum ROI
- Minimum Waste
- Minimum CONC
*The inputs and outputs applicable to the process may vary according to the product process and customer needs and expectations.
APQP - Advanced Product Quality Planning
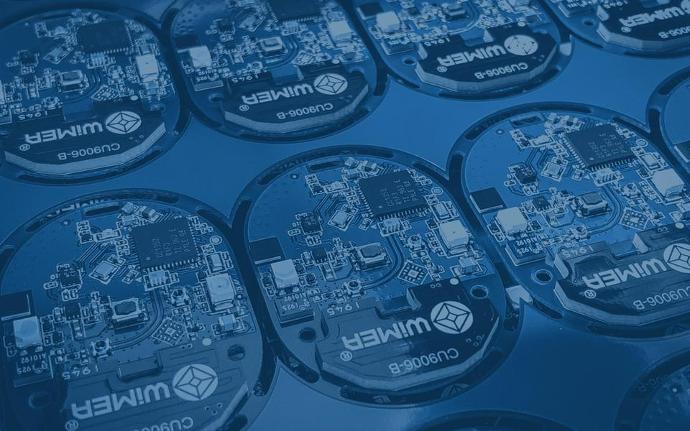
Supplier APQP and PPAP Training Document
This training document is created to educate and guide our valued suppliers through the Advanced Product Quality Planning (APQP) and Production Part Approval Process (PPAP). The purpose is to ensure that all suppliers understand and can effectively implement these processes, ensuring product quality and consistency, in alignment with Fell Tech's high standards and requirements.
Introduction
APQP is the primary Quality Management System in Fell Tech for the Product Development and Engineering Processes.
As a supplier for Fell Tech, it's essential to understand and comply with our required quality processes when they are included in the purchasing or Purchase Order requirements. Two key processes that may be required are the Advanced Product Quality Planning (APQP) and the Production Part Approval Process (PPAP).
Advanced Product Quality Planning (APQP) is a framework of procedures and techniques designed to ensure that the products we develop meet customer needs, expectations, and requirements. It helps to establish a quality plan with the steps to design, develop, and deliver products that satisfy customer expectations. APQP promotes a shared understanding of the necessary steps to ensure that the product development process runs smoothly, on time, and on budget.
On the other hand, Production Part Approval Process (PPAP) is a standardized process in the automotive and aerospace industries that helps manufacturers and suppliers communicate and approve production designs and processes before, during, and after manufacture. PPAP ensures that the processes used to manufacture parts can consistently reproduce the parts at stated production rates during routine production runs.
At Fell Tech, we use these processes to ensure the quality and reliability of the products we purchase from our suppliers. Therefore, we may require you to carry out APQP and PPAP based on the specifics detailed in our Purchase Order requirements. Compliance with these requirements will help in building a strong, reliable, and quality-focused supplier relationship. Please review these processes thoroughly and implement them as needed.
- Advanced Product Quality Planning method to assure that a product satisfies the customer (both internal and external)
- The goal of APQP is to:
- Plan before acting
- Anticipate and prevent issues
- Validate before moving forward
- Facilitate communication
Each Advanced Product Quality Plan is unique and is a living document
Particular emphasis should be placed on identifying critical path activities and ensuring those are fully resourced
APQP Main Purpose
Manufacturing process functions that are clearly planned, validated, documented and communicated that result in:
- Robust and reliable designs
- Reduced process variation
- Enhanced confidence in supplier’s capabilities
- Better controlled process changes
- Defect free launches
- Improved Customer satisfaction
- Improved Delivery and Service
- Maximum ROI
- Minimum Waste
- Minimum Cost of Non-conformance
What are the APQP Development phases?
The Advanced Product Quality Planning process consists of four main phases and five major activities and has some 20+ supporting tools (e.g. DFMEA, PFMEA, CTQ, Special Characteristics, Control Plan, SPC) along with ongoing feedback assessment and corrective action. The phases below is an illustration of a standard APQP process. Fell has developed a specific APQP process and Program Phase Requirements, that can be found here PDE Program Phase Requirements.
All phases needs to go through a Gate Review. The Gate Reviews has predefined check points and necessary documents, tests and validation points that is set for each Gate. The content of the Gate Reviews are determined for each project and determined for each Gate prior to starting a new Phase.
Illustration: Standard Fell APQP Program Timing Chart and Phase Overview.
Validation and Review stages
The stars in the above Timing Chart and Phase Overview illustrates project reviews. These stars indicate a validation of a deliverable, e.g. a prototype or a group documentation for the phase. Typically both. These reviews are always prior to a Gate Review, as the documentation and results from these reviews form the output data going into the Gate Reviews.
- CV = Concept Validation
- DV = Design Validation
- PV = Production Validation
Phases | Scope | X-F Review | X-F Review Goal |
---|---|---|---|
Phase 0 | Input and evaluation | - | Agreement to develop initial business opportunity |
Phase 1 | Definition and planning | - |
|
Phase 2 | Design and Concept Development | Concept Review (CV) |
|
Phase 3a | Design Compatibility | Design Compatibility (DCM) |
|
Phase 3b | Design Validation | Design Validation Review (DV) |
|
Phase 4 | Process Validation | Production Readiness |
|
Phase 5 | Launch | Launch Readiness |
|
1. Plan and Define Program
Purpose
Assure that customer needs and expectations are clearly understood.
Inputs
- Voice of the Customer
- Market Research
- Historical Warranty and Quality Information
- Team Experience
- Business Plan/Marketing Strategy
- Product/Process Benchmark Data
- Product/Process Assumptions
- Product Reliability Studies
- Customer Inputs
Outputs
- Design Goals
- Reliability & Quality goals
- CONC targets
- Preliminary Bill of Materials
- Preliminary Process Flow Chart
- Preliminary list of Special Product and Process Characteristics
- Product Assurance Plan
- Management Support
*The inputs and outputs applicable to the process may vary according to the product process and customer needs and expectations.
Input and Output Documentation
As part of the FELL Quality Management System all relevant templates for the Input and Output documentation is available in Confluence. Typically these are already structured in a project space as part of the tree structure of pages in a project. The easiest way to know that you are selecting a correct template is to only create templates from the "Click To Create" buttons on pages within a project space.
2. Product Design and Development
Purpose
Develop design into a near final form.Prototype and feasibility studies – volumes, schedule, manufacturing.
Inputs
- Design Goals
- Reliability & Quality goals
- Preliminary Bill of Materials
- Preliminary Process Flow Chart
- Preliminary list of Special Product and Process Characteristics
- Product Assurance Plan
Outputs
- Design Failure Mode and Effects Analysis (DFMEA)
- Design For Manufacturability and Assembly
- Design Verification
- Design Reviews
- Prototype Build – Control plan
- Engineering Drawings (Including Math Data)
- Engineering Specifications
- Material Specifications
- Drawing and Specification Changes
*The inputs and outputs applicable to the process may vary according to the product process and customer needs and expectations.
3. Process Design and Development
Purpose
Develop a manufacturing system and its related control plans to achieve quality products.
Inputs
- Design Failure Mode and Effects Analysis (DFMEA)
- Design For Manufacturability and Assembly
- Design Verification
- Design Reviews
- Prototype Build – Control Plan
- Engineering Drawings (Including Math Data)
- Engineering Specifications
- Material Specifications
- Drawing and Specification Changes
- New Equipment, Tooling and Facilities Requirements
- Special Product and Process Characteristics
- Gages/Testing Equipment Requirements
- Team Feasibility Commitment
- Management Support
Outputs
- Packaging Standards
- Product/Process Quality System Review
- Process Flow Chart
- Floor Plan Layout
- Characteristics Matrix
- Process Failure Mode and Effects Analysis (PFMEA)
- Pre-Launch Control Plan
- Process Instructions
- Measurement Systems Analysis Plan
- Preliminary Process Capability Study Plan
- Packaging Specifications
- Management Support
*The inputs and outputs applicable to the process may vary according to the product process and customer needs and expectations.
4. Product and Process Validation
Purpose
Validate manufacturing process through production trial run.
Validate that the control plan and process flow chart are effective and that the product meets customer expectation.
Inputs
- Packaging Standards
- Product/Process Quality System Review
- Process Flow Chart
- Floor Plan Layout
- Characteristics Matrix
- Process Failure Mode and Effects Analysis (PFMEA)
- Pre-Launch Control Plan
- Process Instructions
- Measurement Systems Analysis Plan
- Preliminary Process Capability Study Plan
- Packaging Specifications
- Management Support
Outputs
- Measurement Systems Evaluation
- Significant Production Run
- Preliminary Process Capability Study
- Production Part Approval (PPAP Submission)
- Production Validation Testing
- Packaging Evaluation
- Production Control Plan
- Quality Planning Sign-Off - formal
- Management Support
*The inputs and outputs applicable to the process may vary according to the product process and customer needs and expectations.
5. Feedback, Assessment, Corrective actions
Purpose
Evaluate outputs, effectiveness of the product quality planning efforts.
Inputs
- Production Trial Run
- Measurement Systems Evaluation
- Preliminary Process Capability Study
- Production Part Approval
- Production Validation Testing
- Packaging Evaluation
- Production Control Plan
- Quality Planning Sign-Off and Management Support
Outputs
- Reduced Variation
- Improved Customer Satisfaction
- Improved Delivery and Service
- Effective use of best practice, lessons learned
- Maximum ROI
- Minimum Waste
- Minimum CONC
*The inputs and outputs applicable to the process may vary according to the product process and customer needs and expectations.
Fell Safety Integrity Level (FSIL)
SIL (Fell Safety Integrity Level) is a risk classification scheme derived from ASIL (Automotive Safety Integrity Level), a standard used in the automotive industry. FSIL, however, is adapted to Fell Tech's business sectors, which include marine, building, aerospace, and automotive. It is used to specify the safety integrity requirements of the systems, subsystems, and components within these sectors.
Similar to ASIL, the FSIL levels range from A (lowest) to D (highest), with each level representing the degree of risk involved and the corresponding safety measures required. However, while ASIL primarily focuses on the automotive industry, FSIL extends its application to a broader range of industries, making it more versatile for different contexts.
In addition to physical redundancy, which is the use of multiple instances of a component or system to ensure continued operation if one fails, FSIL also emphasizes the importance of stringent design and process controls. These controls encompass rigorous testing protocols, strict quality control measures, and robust design practices aimed at preventing failures from the outset.
Moreover, FSIL recognizes the value of alternative methods for detecting and mitigating high-severity failures. These can include advanced monitoring systems designed to detect potential failures early, thereby enabling preventative action before a failure occurs. Firmware controls can also be implemented to manage the system's operation and respond to potential issues, such as initiating a system shutdown if a critical failure is detected.
In certain scenarios, if these alternative measures provide a robust enough safety net, physical redundancy may not be required. This is because the alternative measures offer sufficient assurance that high-severity failures will be detected and mitigated, thereby reducing the need for additional physical components or systems as a backup. However, the decision to forego physical redundancy should be made with careful consideration of the potential risks and the effectiveness of the alternative measures.
Here are the revised FSIL levels with the above interpretation:
- FSIL A: Minor safety impact. Basic safety measures are required. The system may have single-point failures, but they do not lead to severe consequences. System redundancy is not typically required at this level. Alternative safety measures such as stringent design and process controls or advanced monitoring systems may be sufficient. This level corresponds to PSW Lvl 4 in the PPAP process.
- FSIL B: Low safety impact. More rigorous safety measures are required. The system should be designed to mitigate single-point failures. Limited redundancy may be required at this level. Alternative safety measures can also be considered. This level corresponds to PSW Lvl 1 in the PPAP process.
- FSIL C: Moderate safety impact. High-level safety measures are required. The system should be designed to tolerate single-point failures. Redundancy is typically required at this level to ensure safety, but alternative safety measures can also be considered. This level corresponds to PSW Lvl 2 in the PPAP process.
- FSIL D: Critical safety impact. Most stringent safety measures are required. The system should be designed to prevent single-point failures. High levels of redundancy are required at this level to ensure safety, but alternative safety measures can also be considered. This level corresponds to PSW Lvl 3 in the PPAP process.
Setting FSIL Level
ASIL (Automotive Safety Integrity Level) is a risk classification scheme defined by the ISO 26262 standard for the functional safety of road vehicles. The standard defines functional safety as the "absence of unreasonable risk due to hazards caused by malfunctioning behavior of electrical or electronic systems". ASILs establish safety requirements based on the probability and acceptability of harm for automotive components to be compliant with ISO 26262. There are four ASILs identified by ISO 26262: ASIL A, ASIL B, ASIL C, and ASIL D. ASIL A represents the lowest degree and ASIL D represents the highest degree of automotive hazard.
The ASIL is established by performing a risk analysis of a potential hazard by looking at the Severity, Exposure, and Controllability of the vehicle operating scenario. The safety goal for that hazard in turn carries the ASIL requirements.
- Severity: The type of injuries to the driver and passengers.
- Exposure: How often the vehicle is exposed to the hazard.
- Controllability: How much the driver can do to prevent the injury.
Each of these variables is broken down into sub-classes. Severity has four classes ranging from "no injuries" (S0) to "life-threatening/fatal injuries" (S3). Exposure has five classes covering the "incredibly unlikely" (E0) to the "highly probable" (E4). Controllability has four classes ranging from "controllable in general" (C0) to "uncontrollable" (C3). All variables and sub-classifications are analyzed and combined to determine the required ASIL. For example, a combination of the highest hazards (S3 + E4 + C3) would result in an ASIL D classification.
Applying this to Fell Tech's business domains, we can define the FSIL (Fell Safety Integrity Level) as follows:
FSIL Level | Severity | Exposure | Controllability | Example (Fell Tech Domain) |
---|---|---|---|---|
FSIL A | Low | Low | High | A minor system in a building that, if it fails, would not cause significant harm and could be easily controlled or mitigated. For example, a non-critical lighting system in a non-essential area. |
FSIL B | Moderate | Moderate | Moderate | A more critical system in an aerospace application that, if it fails, could cause moderate harm but has some level of controllability. For example, a secondary navigation system. |
FSIL C | High | High | Some | A critical system in a marine application that, if it fails, could cause significant harm and is likely to be exposed to the hazard, but there are some controls in place. For example, a primary navigation system in a ship. |
FSIL D | High | High | Low | A vital system in an automotive application that, if it fails, could cause fatal harm, is highly likely to be exposed to the hazard, and has little to no controls in place. For example, a car's braking system. |
Please note that these are general examples and the actual FSIL for a specific system or component would need to be determined through a detailed risk analysis.
PPAP Requirements
Setting PPAP Level from FSIL Level
The FSIL (Fell Safety Integrity Level) and PPAP (Production Part Approval Process) levels are interconnected, providing a comprehensive framework for managing both the safety integrity and the product approval process of systems, subsystems, and components within Fell Tech's business sectors.
FSIL levels, derived from the automotive industry's ASIL (Automotive Safety Integrity Level), are used to specify the safety integrity requirements. They range from A (lowest) to D (highest), with each level representing the degree of risk involved and the corresponding safety measures required.
On the other hand, PPAP levels, a standard part of the automotive industry's quality initiative, are used to provide evidence that all customer engineering design records and specification requirements are properly understood by the manufacturer and that the production process has the potential to produce product consistently meeting these requirements.
The following table presents a correlation between FSIL and PPAP levels, providing a clear understanding of how safety requirements (FSIL levels) align with the production approval process (PPAP levels). This alignment ensures that the safety integrity of a product is maintained throughout its product lifecycle.
FSIL Level | PPAP Level | Description |
---|---|---|
FSIL A | PSW Lvl 4 1) | Minor safety impact. Basic documentation required. |
FSIL B | PSW Lvl 1 2) 3) | Low safety impact. More detailed documentation required. |
FSIL C | PSW Lvl 2 2) 3) | Moderate safety impact. Detailed documentation and sample products required. |
FSIL D | PSW Lvl 3 2) 3) | Critical safety impact. Most stringent documentation and sample requirements. |
FSIL A - D | PSW Lvl 4 1) | Configurable. Can be used for FSIL B, C, and D risk levels. |
- PSW Lvl 4 (lowest level) is configurable in what is Retain and Submit. It shall always be used for non-standard deliveries, meaning it can also be used for FSIL B, C, and D risk levels.
- PSW Lvl 1, 2, and 3 are strictly standardized.
- The PSW level may be changed to less comprehensive levels due to the following reasons:
- The product is already in production and has large statistical confidence in performance and quality since it is sold in large numbers.
- The product is a manufacturer-standard product, and it's not possible to obtain full PPAP due to ownership or non-existence. Confidence is proven in other ways, such as high volumes.
PPAP Requirements Table
Submit vs Retain must be discussed according to the new definition and relation to FSIL level
Requirement | Alternative Name | Description | PSW Lvl 1 | PSW Lvl 2 | PSW Lvl 3 | PSW Lvl 4 |
---|---|---|---|---|---|---|
Documents | ||||||
Design Records If design is owned by supplier | Design Documents | Technical drawings, specifications, or other design-related documents | (R)etain | (R)etain | (S)ubmit | (R)etain |
Design Failure Modes Effects Analysis (DFMEA) - If design is supplier owned | Design Risk Analysis | Analysis of potential failure modes and their impact in the design phase | (R)etain | (R)etain | (S)ubmit | (R)etain |
Process Flow Diagram (PFD) | Process Map | Visual representation of the manufacturing process | (R)etain | (R)etain | (S)ubmit | (R)etain |
Potential Failure Modes Effects Analysis (PFMEA) | Process Risk Analysis | Analysis of potential failure modes and their impact in the manufacturing process | (R)etain | (R)etain | (S)ubmit | (R)etain |
Process Control Plan (PCP) | Control Plan | Plan detailing the process controls used in the manufacturing process | (R)etain | (R)etain | (S)ubmit | (R)retain |
Safe-Launch Process Control Plan | Control Plan
| Plan detailing the process controls used in the start of any new manufacturing process | (R)etain | (R)etain | (S)ubmit | (R)etain |
Dimensional Results of Samples / Sample Inspection Report (SIR)/(SITR) | Sample Inspection Report | Report of the dimensional measurements of the sample parts. Delivered as Initial Sample Inspection Report (ISIR) or similar document.
| (R)etain | (S)ubmit | (S)ubmit | (S)ubmit |
Initial Process Capability Study | Capability Study | Study to determine the production process's ability to meet the part specifications. Min. 30 pcs. required if a Kpc is noted on the drawing. | (R)etain | (R)etain | (S)ubmit | (S)ubmit |
Measurement System Analysis (MSA) | Measurement Analysis | Gage Repeatability & Reproducibility if a KPC is noted on the drawing | (R)etain | (R)etain | (S)ubmit | (S)ubmit |
Checking Aids Description | Inspection Aids | Detaile description of tools or equipment used to inspect the part (Fixtures, gages, test rigs, templates, etc.) | (R)etain | (R)etain | (S)ubmit Changed from Retain to Submit based on our previous experience working with Winner and Huaping | (R)etain |
Material / Performance Test Results | Test Results | Results of material or performance tests conducted on the part. Includes A2LA lab certification if required. | (R)etain | (S)ubmit | (S)ubmit | (S)ubmit |
Appearance Approval Report (AAR) - If applicable | Appearance Check Report | Report of the visual inspection of the part according to specifications from supplier | (S)ubmit | (S)ubmit | (S)ubmit | (R)etain |
Records of Compliance with Customer-Specific - Requirements | Compliance Records Attestation of Conformity Declaration of Conformity | Records showing compliance with customer-specific requirements | (R)etain | (R)etain | (S)ubmit | (R)etain |
Part Submission Warrant (PSW) - AIAG form CFG-1001 | Submission Warrant | Document that summarizes the entire PPAP package | (S)ubmit | (S)ubmit | (S)ubmit | (R)retain |
Samples | ||||||
Cosmetic / Styling Samples -If applicable | Cosmetic Samples | Samples that represent the cosmetic or styling aspects of the part. | (R)etain | (R)etain | (S)ubmit | (R)etain |
Design Validation (DV) Samples | Samples Prototypes
| Physical samples of the part for inspection and Design Validation Testing. Shall be produced by the final production method (e.g. injection molding, stamping).
| Typical 5-25 pc./iteration | |||
Production Validation (PV) Samples | Samples Prototypes | Samples made from final production method at planned run-at-rate and | 200 pc. | 200 pc. | 200 pc. | 200 pc. |
Introduction to Production Part Approval Process (PPAP)
Production Part Approval Process (PPAP) is a valuable tool for establishing confidence in component suppliers and their production processes. In today’s competitive manufacturing environment controlling cost and maintaining a high level of quality have become vital to a company’s success. Increasing costs of equipment, materials and labor combined with expanding world markets have resulted in an increase of outsourced parts. Many component parts are being outsourced to overseas manufacturers. This often results in longer lead times and larger order quantities. Therefore it has become imperative to provide quality parts that meet the customer’s requirements the first time and every time. Initially PPAP was utilized by the automotive and aerospace industries. PPAP is now being utilized by several industries to improve communication and provide quality products. Within the automotive industry the ultimate resource for PPAP information is the manual published by the Automotive Industry Action Group (AIAG).
What is Production Part Approval Process (PPAP)
PPAP defines the approval process for new or revised parts, or parts produced from new or significantly revised production methods. The PPAP process consists of 18 elements that may be required for approval of production level parts. Not all of the elements are required for every submission. There are five generally accepted PPAP submission levels. The PPAP manual contains detailed information, guidelines and sample documents useful for completing the process requirements. The resulting PPAP submission provides the evidence that the supplier has met or exceeded the customer’s requirements and the process is capable of consistently reproducing quality parts.
Why Perform Production Part Approval Process (PPAP)
The PPAP process verifies that the supplier understands all customer engineering design specifications and requirements and that the process is capable of consistently producing product meeting those requirements during an actual production run at the quoted production rate. PPAP and other quality tools continue to be implemented into more industries; therefore it is important to gain an understanding of the PPAP requirements to remain competitive as a parts supplier.
When to Perform Production Part Approval Process (PPAP)
A PPAP is required for any new part submission as well as for approval of any change to an existing part or process. The customer may request a PPAP at any time during the product life. This demands that the supplier must maintain a quality system that develops and documents all of the requirements of a PPAP submission at any time.
How to Perform Production Part Approval Process (PPAP)
The process of completing a PPAP submission is fairly complex. This detailed process is a collection of key elements that must be completed to verify that the production process will produce a quality product. Not all of the elements are always required for a PPAP submission. The particular requirements of the PPAP are usually negotiated during the quoting process.
PPAP Levels of Submission
The PPAP submission requirements are normally divided into five classifications or levels, as follows:
- Level 1 – Part Submission Warrant (PSW) only submitted to the customer
- Level 2 – PSW with product samples and limited supporting data
- Level 3 – PSW with product samples and complete supporting data
- Level 4 – PSW and other requirements as defined by the customer
- Level 5 – PSW with product samples and complete supporting data available for review at the supplier’s manufacturing location
Elements of PPAP
Below is the list of all 19 elements accompanied by a brief description for each element:
- Design Documentation
- Design documentation shall include both a copy of the customer and the supplier’s drawings. The documentation should also include a copy of the purchase order. In some cases the supplier is required to supply documentation of material composition.
- The purchase order is used to confirm that the correct part is being ordered and that it is at the correct revision level.
- The design engineer is responsible for verifying that the two drawings match and all critical or key characteristics have been identified.
- Material composition information is required to supply evidence that the material used manufacture the parts meets the customer’s specific requirements.
- Design documentation shall include both a copy of the customer and the supplier’s drawings. The documentation should also include a copy of the purchase order. In some cases the supplier is required to supply documentation of material composition.
- Engineering Change Documentation
- If the PPAP is being required due to a request for a change to a part or product, the documentation requesting and approving the change must be included in the PPAP package. This documentation usually consists of a copy of the Engineering Change Notice (ECN), which must be approved by the customer engineering department.
- Customer Engineering Approval
- When required as part of the PPAP, the supplier must provide evidence of approval by the customer engineering department.
- If required, pre-PPAP samples are ordered by the customer for onsite testing. The samples must be production intent and ship with a waiver so that testing can be done. When testing is complete, the test engineers will provide an approval form for inclusion in the PPAP submission.
- Note: A copy of a “Temporary Deviation” is normally required to submit parts to the customer prior to a PPAP approval.
- When required as part of the PPAP, the supplier must provide evidence of approval by the customer engineering department.
- Design Failure Mode and Effects Analysis
- Design Failure Mode and Effects Analysis (DFMEA) is a cross-functional activity that examines design risk by exploring the possible failure modes and their effects on the product or customer and their probability to occur. These failure modes can include:
- Product malfunctions
- Reduced performance or product life
- Safety and Regulatory issues
- The DFMEA is a living document that should be reviewed and updated throughout the product life cycle.
- Design Failure Mode and Effects Analysis (DFMEA) is a cross-functional activity that examines design risk by exploring the possible failure modes and their effects on the product or customer and their probability to occur. These failure modes can include:
- Process Flow Diagram
- The Process Flow Diagram outlines the entire process for assembling the component or final assembly in a graphical manner. The process flow includes incoming material, assembly, test, rework and shipping.
- Process Failure Mode and Effects Analysis
- Process Failure Mode and Effects Analysis (PFMEA) reviews all of the steps in the production process to identify any potential process quality risk and then document the applied controls. The PFMEA is also a living document and should be updated even after the product is in normal production.
- Control Plan
- The Control Plan is an output from the PFMEA. The Control Plan lists all product Special Characteristics and inspection methods required to deliver products that continually meet the customer quality requirements.
- Measurement System Analysis Studies
- Measurement System Analysis (MSA) studies will include Gage Repeatability & Reproducibility (GR&R) studies on measurement equipment used during assembly or quality control checks. Calibration records for all gages and measurement equipment must be included.
- Dimensional Results
- Dimensional layout of sample parts is required to validate the product meets the print specifications. The samples should be randomly selected from a significant production run usually at least 30 pieces. Each dimension on the drawing is measured on the final assembly to make sure that it falls within specification. The results are recorded in a spreadsheet and included within the PPAP submission.
- Records of Material / Performance Tests
- This element should contain a copy of the Design Verification Plan and Report (DVP&R). The DVP&R is a summary of every validation test performed on the part. It should list each and every test performed, a description of how the test was performed, and the results of each test.
- This section may also include copies of all the certification documents for all materials (steel, plastics, etc.) listed on the prints. The material certification shall show compliance to the specific call on the print.
- Initial Sample Inspection Report
- The report for material samples which is initially inspected before prototype made
- Initial Process Studies
- Initial process studies will be done on all the production processes and will include Statistical Process Control (SPC) charts on the critical characteristics of the product. These studies demonstrate that the critical processes are stable, demonstrate normal variation and are running near the intended nominal value.
- Qualified Laboratory Documentation
- Qualified laboratory documentation consists of the industry certifications for any lab that was involved in completing validation testing. This could be for an in-house test lab or any offsite contracted test facilities that were used for validation or material certification testing.
- Appearance Approval Report
- The Appearance Approval Inspection (AAI) is applicable for components affecting appearance only. This report verifies that the customer has inspected the final product and it meets all the required appearance specifications for the design. The appearance requirements could include information regarding the color, textures, etc.
- Sample Production Parts
- Sample production parts are sent to the customer for approval and are typically stored at either the customer or supplier’s site after the product development is complete. A picture of the production parts is usually included in the PPAP documentation along with documentation regarding the location that the parts are being stored.
- Master Sample
- A master sample is a final sample of the product that is inspected and signed off by the customer. The master sample part is used to train operators and serves as a benchmark for comparison to standard production parts if any part quality questions arise.
- Checking Aids
- This is a detailed list of checking aids used by production. It should include all tools used to inspect, test or measure parts during the assembly process. The list should describe the tool and have the calibration schedule for the tool. Checking aids may include check fixtures, contour, variable and attribute gages, models or templates.
- MSA may be required for all checking aids based on customer requirements.
- Customer Specific Requirements
- This element of the submission package is where any special customer requirements are contained. For bulk materials, the customer specific requirements shall be recorded on the “Bulk Material Requirements Checklist”.
- Part Submission Warrant
- The Part Submission Warrant (PSW) form is a summary of the entire PPAP submission. A PSW is required for each of part number unless otherwise stated by the customer. The PSW includes:
- The reason for submission (design change, annual re-validation, etc.)
- The level of documents submitted to the customer
- Declaration of part conformity to customer requirements
- A section provided for any required explanation or comments
- Supplier authorized person signature along with contact information
- An area for the customer to indicate disposition of the PPAP
- The Part Submission Warrant (PSW) form is a summary of the entire PPAP submission. A PSW is required for each of part number unless otherwise stated by the customer. The PSW includes:
The PPAP process is a detailed and lengthy process. The PPAP package includes documentation of various multiple cross-functional tools and documents the ability of the supplier to meet all customer requirements. PPAP provides customers adequate information to validate that all areas of the design and production processes have been reviewed thoroughly to ensure that only high quality products will be allowed to ship to the end customer.
PPAP Submission and Part Submission Warrant (PSW)
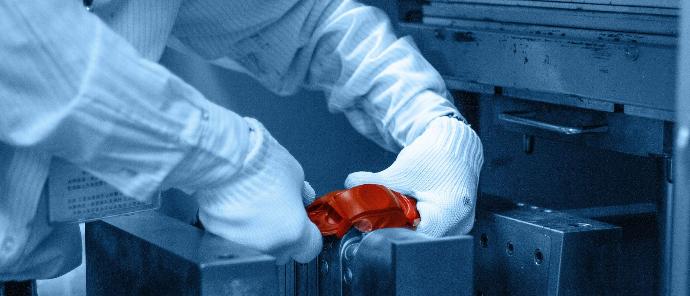
PPAP Submission Documents Templates
The PPAP Submission Documents Templates are designed to provide a structured and standardized format for suppliers to submit their Production Part Approval Process (PPAP) documentation. These templates aim to streamline the submission process, minimize errors, and ensure that all required information is accurately captured and presented in a way that is consistent with Fell Tech's requirements.
About PPAP Submission
The Production Part Approval Process (PPAP) is a crucial part of the manufacturing process in various industries, including automotive and aerospace. This standardized procedure helps to ensure that the supplier understands all of the customer's specifications and requirements and can meet them consistently. It establishes a clear line of communication and understanding between suppliers and manufacturers, which helps to prevent issues and misunderstandings that could impact the product's quality or the delivery timeline.
At the core of the PPAP process is the Part Submission Warrant (PSW). This document serves as a summary and proof of the entire PPAP package. It verifies that the supplier has comprehensively reviewed and tested their product to ensure it meets all design specifications and quality requirements.
In essence, the PSW acts as the supplier's commitment to delivering a product that meets all defined criteria, and it's the key document that manufacturers look for in a PPAP submission. It should contain details about the product, including the part name and number, the supplier's details, information about the manufacturing process, and the results of various analyses and tests conducted on the part.
Creating a PSW involves a series of meticulous steps. The process starts with a complete and in-depth review of the product design to ensure it aligns with the customer's requirements. The supplier then needs to carry out a series of tests and analyses to validate that the product can be manufactured consistently and to the desired specifications. This includes the Design Failure Modes and Effects Analysis (DFMEA), the Process Failure Modes and Effects Analysis (PFMEA), and the Control Plan.
These analyses aim to identify potential risks and issues before production starts. They ensure the manufacturing process is robust enough to deliver the required quantity of parts without compromising the quality. If any risks are identified during these analyses, the supplier is expected to take corrective actions and validate them before proceeding with production.
Once all the analyses are complete, and the parts have been validated, the supplier compiles all the information and documentation into the PSW. This document is then submitted to the customer for review and approval. If the PSW is approved, it signifies that the customer is satisfied with the part's design and the supplier's manufacturing process, and production can begin.
Please contact a Fell Tech quality or purchase representative with any questions regarding a PPAP submission.